Discovering the Different Methods of Aluminum Spreading: A Comprehensive Guide
Light weight aluminum casting stands as a fundamental procedure in the development of numerous items we encounter daily, from detailed automobile components to family fixtures. Understanding the diverse techniques made use of in light weight aluminum casting is critical for producers looking for accuracy and effectiveness in their manufacturing processes - aluminum casting. As we start this exploration of the different techniques associated with light weight aluminum casting, we reveal a world where technology and custom merge to shape the products that form our modern world
Sand Spreading Method
Using among the earliest and most extensively utilized approaches in light weight aluminum casting, the sand casting approach involves producing mold and mildews from a mixture of sand and a binder material. This technique is extremely functional, cost-effective, and appropriate for creating a variety of shapes and dimensions, making it a popular option in numerous sectors.
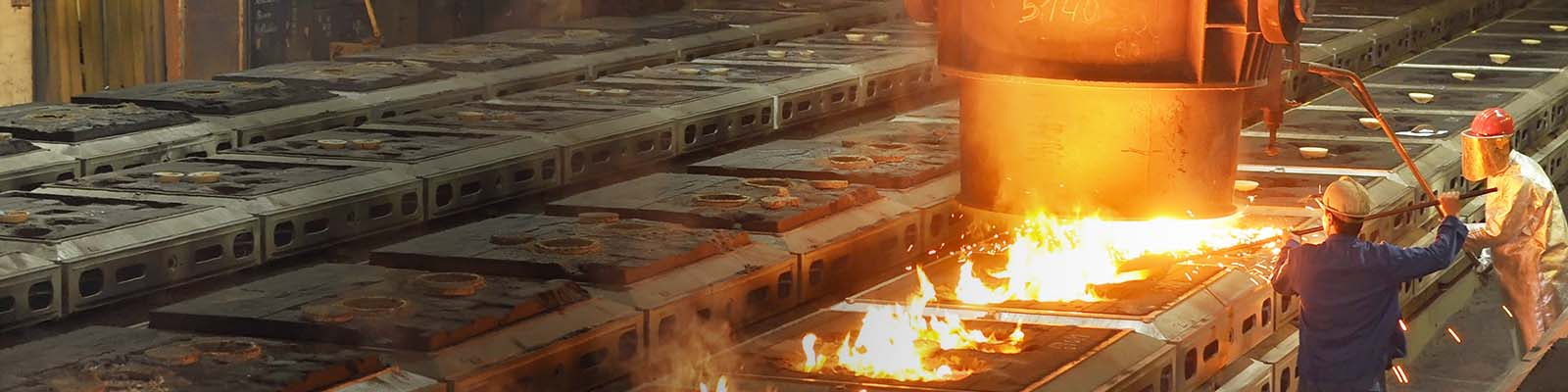
Aluminum, warmed to its melting factor, is then put into the mold and mildew, filling up the cavity. After cooling down and solidifying, the sand mold and mildew is broken away, disclosing the aluminum spreading. This technique enables the manufacturing of complicated geometries and is fit for both high and reduced volume manufacturing runs.
Investment Casting Method
Having checked out the sand casting method, a polished strategy to aluminum casting is the investment spreading strategy, which offers distinct advantages in terms of accuracy and surface area coating. Financial investment spreading, also known as lost-wax casting, is a procedure that entails developing a wax pattern that is covered with a ceramic covering.
One of the main benefits of investment casting is its ability to create complicated shapes with high precision and complex information. The procedure enables slim wall surfaces, sharp edges, and fine surface finishes that require very little post-processing. Furthermore, investment casting is known for its outstanding dimensional accuracy and tight resistances, making it a recommended approach for generating components that need tight specs. In general, the investment casting technique is a reliable and flexible technique for manufacturing premium aluminum components.
Long-term Mold And Mildew Refine
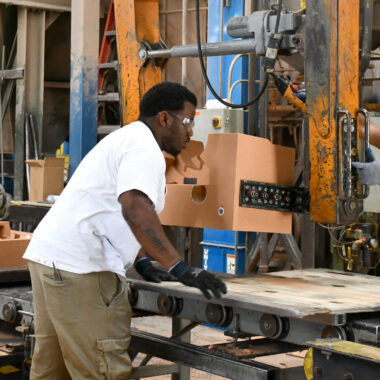
One of the crucial benefits of the Long-term Mold And Mildew Process is its capability to generate parts with a finer grain framework, resulting in boosted mechanical homes. By leveraging the Irreversible Mold Process, suppliers can achieve economical manufacturing of aluminum parts with exceptional dimensional precision and surface finish.
Die Casting Strategy
In contrast to the Permanent Mold Refine, the Pass Away Casting Approach for aluminum casting includes making use of a multiple-use steel mold to produce elaborate get rid of high dimensional precision. This approach is extensively used in various markets because of its capability to successfully manufacture intricate forms with slim wall surfaces and excellent surface finishes.
Die casting generally begins with the preparation of the steel mold, which is then sprayed with a lubricant to help with the removal of the solidified aluminum. The mold is shut, and molten light weight aluminum is infused under high stress right into the tooth cavity. When the aluminum solidifies and cools, the mold and mildew opens up, disclosing the completed part.
One of the essential advantages of die spreading is its high manufacturing price, making it a cost-efficient remedy for large production. Furthermore, parts produced via die spreading display exceptional strength and resilience compared to those made via various other casting techniques. This method is particularly ideal for applications needing elaborate designs, limited resistances, and high repeatability.
Centrifugal Casting Approach
Exactly how can the Centrifugal Casting Approach improve the effectiveness and quality of light weight aluminum casting procedures? Centrifugal spreading is a method that makes use of centrifugal pressure to distribute liquified metal right into a mold cavity. This strategy provides several benefits over conventional spreading techniques.
One key advantage is the superior top quality of the castings generated. The centrifugal force aids to get rid of porosity by pressing any type of gas or contaminations towards the facility of the casting, resulting in a denser and a lot more uniform end product (aluminum casting). Furthermore, the rotational motion of the mold and mildew ensures an extra even distribution of the liquified metal, bring about improved mechanical residential properties and reduced problems
Additionally, the Centrifugal Casting Technique is known for its performance. The rapid solidification price attained through this procedure can add to shortened cycle times, making it a cost-efficient solution for high-volume manufacturing. Furthermore, the approach enables the casting of complex forms and thin-walled parts with simplicity, increasing the design possibilities for producers. In verdict, the linked here Centrifugal Spreading Method stands apart as a trusted strategy for enhancing both the efficiency and high quality of aluminum spreading procedures.

Verdict
In conclusion, the numerous methods of light weight aluminum casting supply unique advantages and features for different applications. Sand spreading provides adaptability and cost-effectiveness, investment casting permits elaborate layouts, permanent mold procedure guarantees high-grade finishes, pass away casting gives high production rates, and centrifugal spreading generates high-strength components. Comprehending the distinctions in between these methods can assist suppliers pick the most appropriate strategy for their particular spreading demands.
Having checked out the sand spreading approach, a polished approach to aluminum casting is the investment casting method, which uses distinctive benefits in terms of accuracy and surface area coating. Financial investment spreading, also known as lost-wax casting, is a process that involves creating a wax pattern that is coated with a ceramic shell.How can the Centrifugal Casting Method go to this web-site enhance the efficiency and quality of aluminum casting processes? In conclusion, the Centrifugal Spreading Approach stands out as visit site a reliable technique for enhancing both the efficiency and quality of light weight aluminum spreading procedures.
Sand casting provides flexibility and cost-effectiveness, investment spreading permits for complex styles, long-term mold procedure makes certain high-grade coatings, pass away casting offers high production prices, and centrifugal spreading produces high-strength components.